Do you want to start a solar panel manufacturing factory and you need an in-depth solar panel manufacturing plant cost breakdown? If yes, then you are at the right place. In this article, we will give details of the following costs:
- Machinery costs for solar panel manufacturing equipment (investment)
- Costs of building for your solar module production line (investment)
- Costs for infrastructure (investment)
- Cost for material in stock (working capital)
- Cost for production per watt (material cost + operating costs)
Working capital is necessary for solar panel production because you need to purchase materials before producing the panels, and only then can you sell them. In this article, we will make rough estimations for material working capital. Please keep in mind that these figures represent cash flow requirements for production, not actual costs.
Different Sizes for PV Production Plants
Solar (PV) production machines come in a wide range of sizes. You can start with a very small line (for example, 25 MW) using refurbished equipment, or you can opt for brand new machines.
Brand new machines range from 50 MW (the smallest size) to fully automated lines with 1 GW capacity or more.
A smaller plant like a 25 MW plant will require a smaller investment. A good size to start with for new equipment will be 100 MW or more.
In this article, we will discuss the following examples:
- 25 MW line with refurbished equipment
- 100 MW line with new machines
- 600-800 MW line new, fully automated line
Of course, we are offering customized solar module production lines for all sizes and demands; therefore, if you are interested in a customized offer for you, please send a request with our contact form >>
Machinery Investment for a Solar Module Production Line
The investment that you need depends on three main points:
- Refurbished machines (cheaper) or new equipment (more options)
- The size of the solar module manufacturing line
- The automation of the solar module production
Refurbished Machines
For refurbished machines, you can significantly lower your investment. For example, a line with 25 MW capacity would require an investment of only 250,000.00 € (two hundred fifty thousand euros) for the machines. However, you will be limited in the panel types you can produce and will not be able to manufacture using the latest technology.
On the other hand, this is a good opportunity to start production, test the market, and begin sales without taking on the significant risk of a large investment.
We recommend refurbished equipment if you want to enter the market, learn the process, and avoid investing and risking too much money. Refurbished solar machinery can be an excellent opportunity to start, especially in areas with low salaries and markets demanding smaller-sized panels.
New Machines for Solar Module Production
If you want to start with the latest technology and high automation, then you need to opt for new solar production machines. These new machines will be capable of producing the latest technology, for example:
- 650 (and more) watt panel design (210 mm wafer)
- 550 (and more) watt panels design (182 mm wafer)
- Half cut designs
- Third cut designs
- All technologies like PERC, PERCT, TopCon, HJT
- Multi bus bar technology
Automation will be significantly higher for new equipment compared to refurbished units, but the cost will also be substantially greater.
You can start with a new line from about 50 MW, but 100 MW will be more effective.
For example, a medium automated 100 MW line would cost approximately 1.5-2 million Euros. Prices vary based on the level of automation and technology used. If you are interested in an offer for a new line, please make a request with the desired size, and we will provide an individual offer: Contact >>
Building Investment for a Solar Panel Factory
Additional to the machinery investment, you have to consider the investment you need for the building for:
- Production area where you place the machines
- Stock for incoming material
- Stock for outgoing material (ready made panels)
- Infrastructure (air condition, compressed air, electrical power supply)
Here, we will give you some examples for 3 typical solar module production line sizes:
20-25 MW Refurbished Equipment Solar Factory
For a small, refurbished production line, we believe it doesn’t make financial sense to construct a building yourself because:
- Only a small building is needed, for example, about 500-800 sqm.
- You will likely extend your factory in the future, and then your building may be too small for a new line.
Therefore, let’s assume you rent a building and only invest in the infrastructure, which would cost approximately €100,000 (one hundred thousand euros).
100 MW New Solar Factory
It might be challenging to find a building that matches your 100 MW line. While renting a building is an option, in our experience, most investors prefer to construct a new building for a 100 MW solar production line.
For a 100 MW line, including storage and office space, you would need a building of about 1,000 sqm. Prices vary based on the country where the building is located, but let’s estimate the cost at approximately €1.5 million.
600-800 MW New
For a factory with a capacity of up to 800 MW, you will need a building of about 5,500 sqm, which could cost approximately €6 million. Please note that prices vary based on the country where the building is located.
Invest for Prefinancing
As with any business, you will need initial capital for:
- Working capital (materials for solar module production)
- Initial salaries (e.g., during the building phase)
- Initial losses (as you ramp up the factory)
We will now provide approximate figures for the three sizes specifically discussed in this article.
20-25 MW
A small production line also requires a small amount of working capital. Our rough estimate is €100,000 (one hundred thousand euros).
100 MW Line
For a 100 MW line, we are calculating with a bit more stock to lower the risk of potential production stoppages. Therefore, you can estimate the cost to be approximately €800,000 (eight hundred thousand euros)
800 MW Production Line
To ensure you have enough stock to avoid stopping production due to a lack of materials, you should estimate approximately €6.5 million for working capital, including materials in stock.
Manufacturing Cost: Material
Percentage of Material Compared to Total Production Costs of Solar Modules
The cost of materials for solar panels constitutes over 95% of the total production costs, making it the dominant factor in solar module production.
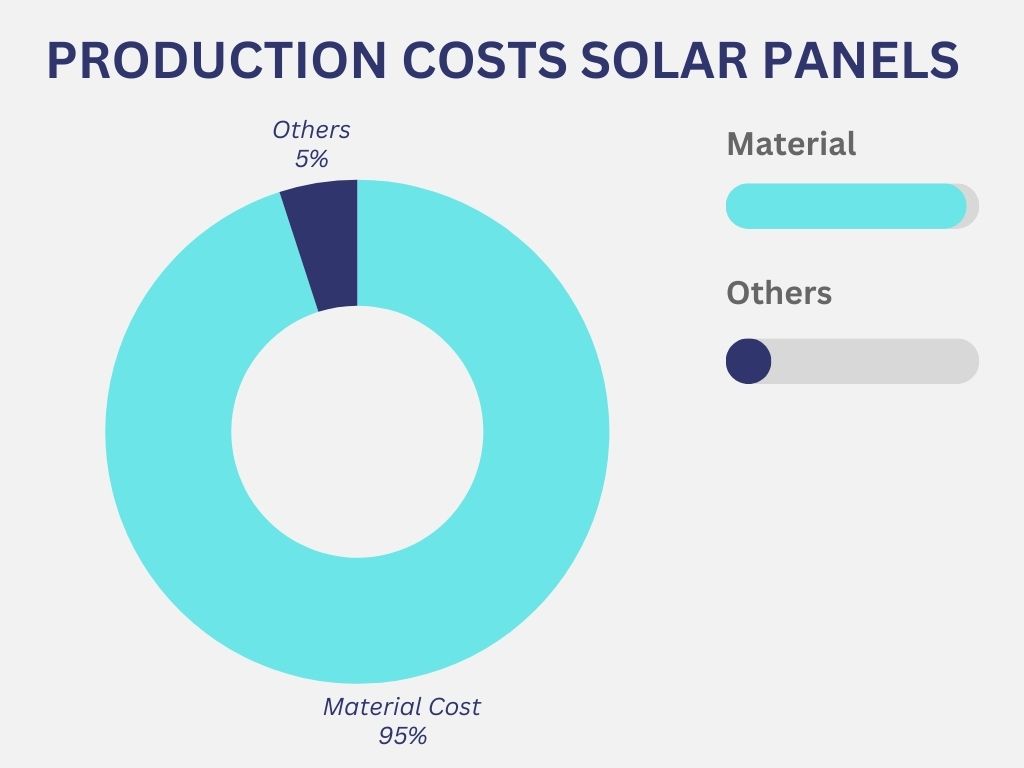
Manufacturing costs of solar module production
Materials for Solar Panel Manufacturing
The following materials are needed for your solar module production factory:
- Glass for front side
- Embedding foil 1
- Solar cells
- Ribbons (connector wires for the solar cells)
- Interconnection ribbons (the bussing ribbon to connect the strings)
- Embedding foil 2
- Backsheet (or backside glass for glass-glass-panels)
- Junction box and diode and connectors
- Aluminium frame set
The main costs for the materials are solar cells (more than 40%), glass (about 20%), and aluminum (14%). Below, you can find a picture showing the percentage of each material.
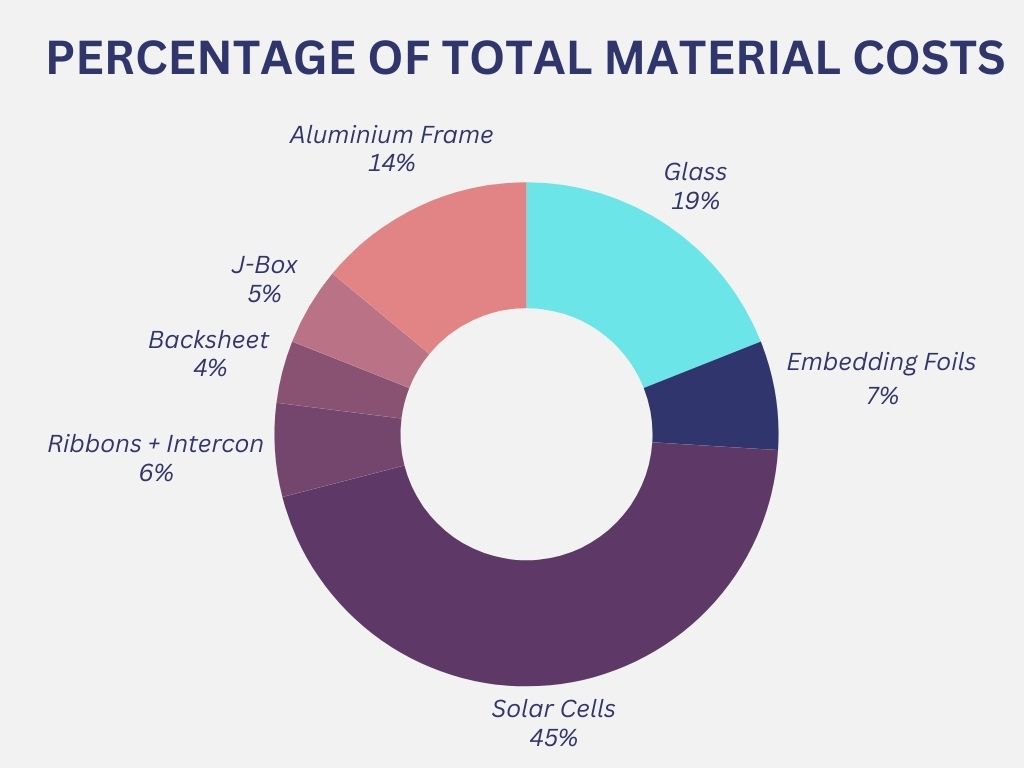
solar panel manufacturing plant cost breakdown of the total material costs
Manufacturing Cost: Overheads
Overhead Cost Definition
The overheads or overhead costs are the operating expenses of a factory and mainly consist of:
- Human resources
- Depreciation of CAPEX (machines, building, other investments)
- Running costs of factory (maintenance, energy costs, financing costs and so on)
While materials are a major cost factor in production, overhead costs range from 3% to 12% of the total manufacturing costs, depending on the size of production.
Overhead Costs by Factory Size
Below, you will find rough estimations for the overheads in US-Dollar-Cent per each watt for different factory sizes:
- 25 MW factory: Overheads between 1-2 Dollar Cents / watt
- 100 MW factory: Overheads about 1 Dollar Cent / watt
- 400 MW factory: Overheads about 0.5-0.9 Dollar Cent / watt
- 800 MW factory or above: Overheads about 0,5 Dollar cent / watt or lower!
Please note: The quality of the equipment you buy is only a small part of production costs! Based on the produced wattage, a high-quality production line with a capacity of 500 MW or more from Germany compared to a low-quality, cheaper line from elsewhere will result in nearly no difference in the cost per watt for the produced solar panels.
Miseensa
Very good information for beginners
Bonjour,
Pourriez vous m’indiquer approximativement les coups liés au transport (aussi bien pour les machines que pour les matériaux)?
Exemple : République du Tchad ( en Afrique centrale) dont le port le plus proche est celui de Douala (en République du Cameroun).
Very good
Very good
شكرا جزيلا
Hello dear
I am a chemical engineer in petrochemical industries. I have a master’s degree in executive management and am currently a PhD student in human resources management. I have managed the Borhan Law Firm for many years and have experience in the power plant and petrochemical industries. I currently sell stock generators belonging to Caterpillar, Cummins, Benzo Scania, etc. in part of the company. Currently, there is a problem of power outages in Iran and there is a good market and potential for this issue. I have all the facilities, including labor and installation, storage space and warehouse, initial capital, a legal department called Borhan Law Firm, which allows me to enter into various contracts with buyers, etc. Honesty in speech and trustworthiness in secrets, facilities, and technology are the mainstays of my company.Currently, I have several orders in Iran in the field of solar panels and solar power plants. I have done several small projects in Ilam, Shahmirzad and Chabahar as an intermediary. Competitive advantage in price, type and quality of panels and differentiation in the market are very important, and after-sales service and necessary incentives to attract customers require the support of the company. The possibility of receiving capital even from government sources in this regard, considering that this year in Iran, the supply of part of the electricity of industries by renewable energies and solar panels has become mandatory, and the circular announced by the Ministry of Energy and the Iranian Electricity Company is available, which I am sending.
I have a very suitable market for the construction of solar power plants in Iranian industries and even on a small scale in villas and agricultural sectors. I have and have a wide range of marketing and communication capabilities.
My request is, firstly, what are the conditions for receiving representation from your company, and secondly, what are the preparations and facilities required for this. Please provide the necessary conditions.
My email is hassanmardi42@gmail.com
Contact number 00989127614300 and my office number is 00982143999 My office address is Tehran _Sattari Highway _Mokhbari Street _ Opposite the Administrative Court, No. 188, Unit 6 and my second office is Tehran, Valiasr Street _ not reaching Tajrish Square, corner of Sarshar Alley, upper floor of the National Bank of Iran, Unit 3
I am able to provide any necessary documents and documentation.
Regards,
Hassan Mardi
Executive Director of Noavaran Sarzam Bardia Company
Hi Hassan Mardi, thanks for reaching out. please send a message here: https://solar.jvg-thoma.de/
Can we collaborate in partnership in setting up a manufacturing plant here in Nigeria? We can facilitate that partnership here
Dear Mr Ogunbanjo I m interesting with to set up solar systems in NiGEiA
Please contact with me by e-Mail metin.karakas@alcibay.com or WhatsApp +90 533 662 70 94
Regards
Would you arrange finance for The Solar Power to be Generated in more than 100MW? I would be obliged if you would answer me soon. I need to install Solar Panels for Power Generation in my Country. We’ve been in Hydro Power Development since 1998. If we could arrange a good deal, I believe we can work together. I would need to Install some SolarPower Plants of Huge Capacity of more than 100 MW, if you could work in BOOT basis, I would represent you and get you deals. We need to work on cutting Cost as well.
Could we do that?
Hi, thanks for reaching out to us. Please send us a detailed message via this link:
https://www.jvg-thoma.de/contact/
Can you help us find a joint venture partner from Germany for solar panel manufacturing in india
Hi, contact us here for more inquiries: https://www.pvknowhow.com/contact/
I am new in the game I am in South Africa and I want more information about the factory startup and requirements thereof
Hi, thanks for reaching out to us. Please send us a detailed message via this link:
https://solar.jvg-thoma.de/
Very good information for new solar panel manufacturing business
Hi there, this is very interesting, I would like to startup a solar manufacturing plant here in Namibia, are there any franchises on solar panel production companies that you can recommend??
Hi, please send us a message via: https://solar.jvg-thoma.de/
Hello , I would love to invest in buying and operating a medium size solar panel production line , either here in the USA or in Egypt, where I am originally from.
I am new to the field , but I recently come back to the USA from a visit to China, where I visited some factories for solar panels, lithium batteries and inverters.
Need help , you can contact me directly by phone +19102746085.
Thank you in advance
Magdy Farag
Hi, please send us a message via: https://solar.jvg-thoma.de/
I am interested in collaboration/partnership to set up a Solar Panel Manufacturing plant in a Free Trade Zone in Nigeria.
Hi, please send us a message via: https://solar.jvg-thoma.de/
Partnership collaborate and to facilitate a manufacturing plant in South – South Nigeria.
Hi, please send us a message via: https://solar.jvg-thoma.de/
Can the industry be run on Solar itself?
Ok
Good morning sir I am interested solar panel mansuring company
Impressive energy to be global production
Hey am much interested for partnership here in Botswana
Please show equipment catalogue ,
equity161@gmail.com
What’s the current bom cost per watt ?
For topcon solar module.
I am interested in setting up a solar panel manufacturing plant in Nigeria.