The energy world is changing quickly because solar power is becoming more and more important. The demand for solar panels is increasing, and there is a need for production processes that are fast, effective, and reliable. One big challenge is laminating the solar cells, which makes them strong against temperature changes and helps them work better.
This article dives into the existence of solar panel laminators, stating their role, functionality, types, and fundamental aspects that concern the manufacturers of solar panels.
What is a Solar Panel Laminator?
A solar panel laminator is a machine that is used to make solar panels. This machine uses heat and pressure to stick different layers of the photovoltaic module together. The laminator makes sure that the solar cells are sealed within the protective layers of the solar module, creating a strong bond.
The laminator plays a very important role in making sure the solar panel is strong and protected from the environment. It covers the solar cells with a layer of glass on top and a layer of polymer underneath, usually using a special adhesive called ethylene-vinyl acetate (EVA).
A machine called a PV laminator is very important for making sure that the solar product is good quality, works well, and lasts a long time.
These layers typically include:
• Tempered glass: Creates a protective layer that is in the front of the solar panels.
• Encapsulant (usually Ethylene Vinyl Acetate - EVA): Fills the gaps between cells and protects cells from environmental effects i.e. dust.
• Solar cells: Solar panels as the engine, changing sunlight into electricity.
• Back sheet: Seals back the module and provides extra security.
Key Component of Solar Panel Laminator
During production, solar panel laminators use heat and pressure to bond different layers of a solar panel together, creating a durable and weather-resistant unit. Here are the main parts of a solar panel laminator.
Heating System
Heating elements are really important when making solar panels. They help melt the polymer films that stick the layers and solar cells together. Encapsulants like Ethylene Vinyl Acetate (EVA) protect the solar cells by melting and covering them. There are different types of heaters used, like infrared heaters, thermal oil heaters, and electric heater elements. The encapsulant usually melts at temperatures between 135°C and 150°C, making sure the solar cells are safe and last a long time.
Vacuum Chamber
The vacuum chamber is really important for getting rid of air bubbles when putting the encapsulation on solar cells. This step is super important for making sure the encapsulant sticks properly to the cells. If you don't use a vacuum chamber, air bubbles and dirt can make the solar panels less efficient and not last as long. The vacuum chamber takes out the air and dirt, so the encapsulation goes on smoothly without any bubbles.
Pressure Rollers
Pressure rollers are used in laminators to make sure the pressure is the same all over the solar panel. This helps to spread the protective layer evenly over the solar cells. The protective layer keeps the cells safe and helps them stick to the glass or plastic layers. Getting the right amount of pressure is really important for making sure the solar panels last a long time and work well.
Cooling System
After the solar panel is laminated, it needs to be cooled quickly to make sure the layers stick together well. A cooling system is important for cooling down the hot platens used in lamination. Usually, a pump circulates cold water through a heat exchanger and into the hot platen fluid to take away the heat. The cooled fluid then goes back to the platens, lowering their temperature and making sure the solar panel hardens correctly without bending or getting stressed inside.
Control System
The control system in a laminator is in charge of managing the pressure, temperature, and vacuum inside the laminator chamber. It also controls the timing of the lamination process to make sure each step is done correctly every time. New control systems let you make very exact changes and keep an eye on things, which is really important for making sure the lamination process is good quality and dependable.
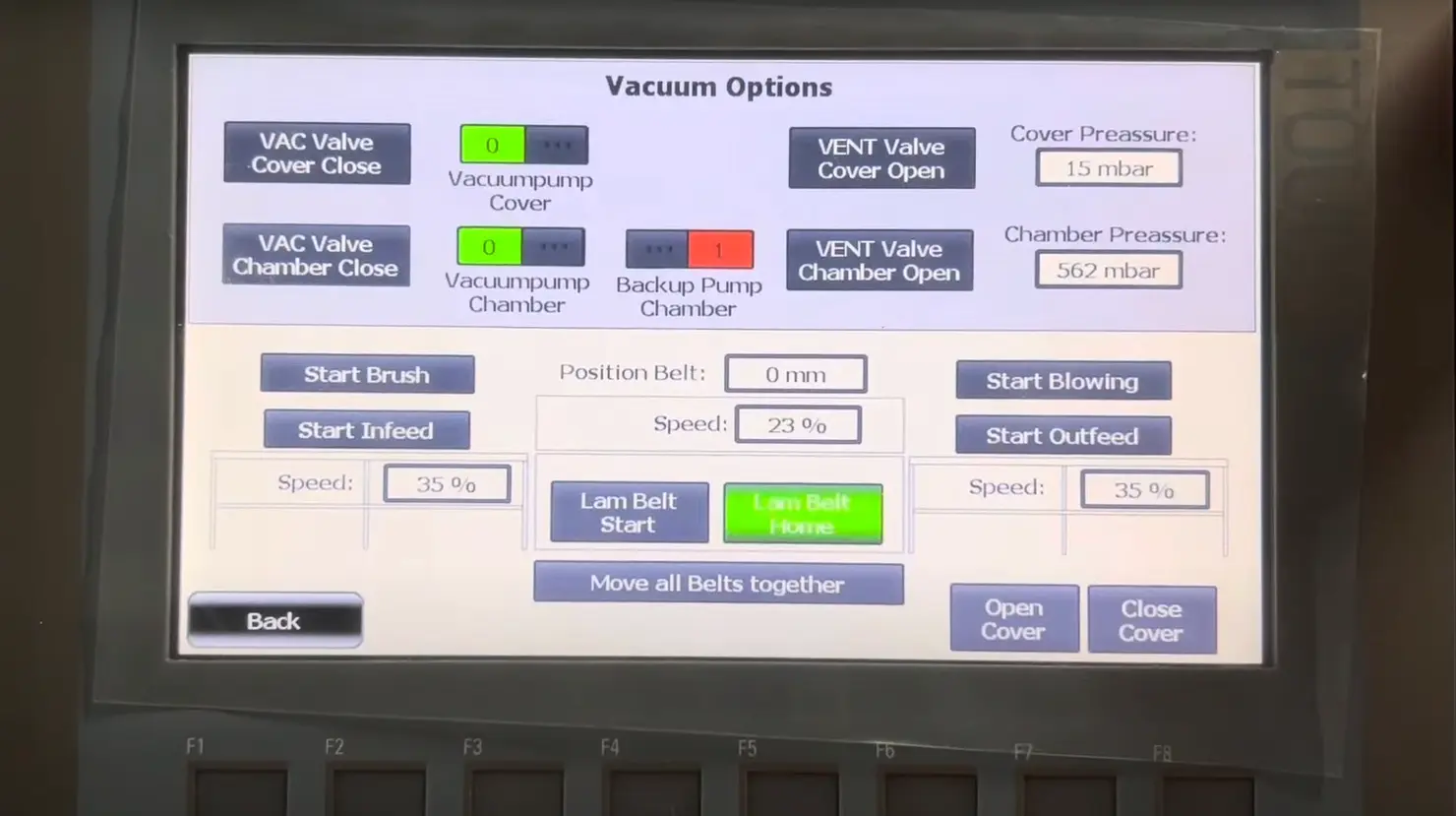
control panel of a solar module laminator
Types of Solar Panel Laminators
There are two main types of lamination machines 1. Semi-Automated PV Laminators & 2. Fully Automated PV Laminators, each with distinct features, pros, and cons:
Feature | Semi-Automatic PV Laminators | Fully Automatic PV Laminators |
---|---|---|
Automation Level | Partial automation; some tasks automated, but human intervention required for others | High level of automation; minimal human intervention required |
Loading/Unloading | Manual loading and unloading of components | Fully automated robotic handling for loading and unloading |
Control System | Intermediate control systems; some automated controls | Advanced computer control systems for precise management of temperature, pressure, and vacuum |
Temperature Regulation | Semi-automated temperature control | Fully automated temperature regulation |
Pressure Application | Semi-automated pressure application | Fully automated pressure application |
Vacuum System | Semi-automated vacuum system | Advanced vacuum system with automated control |
Production Volume | Suitable for medium-sized production environments | Ideal for large-scale industrial production |
Efficiency | Moderate efficiency; balance between manual and automated processes | High efficiency due to full automation |
Quality Consistency | Improved quality consistency; some automation ensures better control | High quality consistency; automated systems ensure uniformity |
Initial Investment | Moderate initial investment | High initial investment |
Operational Costs | Moderate operational costs | Lower operational costs in the long term due to reduced labor and increased efficiency |
Maintenance Requirements | Moderate maintenance requirements | Higher maintenance requirements due to complex automated systems |
Best Suited For | Medium-sized production environments aiming for a balance between cost and efficiency | Large-scale industrial production where high output volume and consistent quality are required |
Semi-Automatic PV Laminators
Semi-automatic solar panel laminators combine manual and automated processes. Operators manually load the solar cells, encapsulant materials, and cover sheets into the machine. The machine then automates certain tasks, such as temperature control and pressure application, but still requires human intervention for loading and unloading components.
- Pros:
- Balance between automation and manual intervention.
- Suitable for medium-sized production environments.
- Improved efficiency over manual laminators.
- Moderate initial investment.
- Cons:
- Requires human intervention.
- Not as fast or efficient as fully automatic laminators.
- Moderate operational and maintenance costs.
Fully Automatic PV Laminators
Fully automatic solar laminators represent the pinnacle of efficiency and automation in solar module manufacturing. These machines use robotic handling technologies for loading and unloading modules and integrated computer control systems to manage the entire lamination process, including temperature regulation and pressure application.

large full auto photovoltaic module laminator
- Pros:
- High degree of automation.
- Consistent quality.
- High productivity and throughput.
- Lower operational costs in the long term.
- Cons:
- High initial investment.
- Requires significant setup and maintenance.
- Higher maintenance requirements due to complex automated systems.
Detailed Solar Module Lamination Process
Solar module lamination is a procedure that involves the placement of solar cells between layers of material with the intention of not only providing protection but also weather resistance to the module. However, this is of utmost importance because it protect the components from the environment, like moisture, dust, and contact stress. There are three major steps which are basically divided into seven steps for complete lamination process within a solar laminator such as:
1. Assembly: The cells are tightly connected on a back sheet which is placed on the frame. Other than the encapsulant and tempered glass, the setup is completed.
2. Loading: In the case of laminating, the whole collection is loaded into the laminator.
3. Vacuuming: The air is sucked out, thus, the pockets of air that may interfere with performance are discarded.
4. Heating: The chamber is heated at a precise temperature, ranging from 140oC to 180oC, depending on the particular material of encapsulant. This leads to the generation of the adhesive features of the underlying encapsulant.
5. Pressurization: The chamber must be pressurized to get all the encapsulants thoroughly spread over the layers, as well as to create a strong bond between them.
6. Cooling: The room is cooled down to irreversibly set the state of the encapsulant and achieve the desired form of the finished solar panel.
7. Unloading: The laminator extracts and removes the final solar panel.
Here in this video a solar laminator from J. v. G. technology GmbH is working on laminating a solar panel.
Benefits of Photovoltaic Module Lamination
The lamination process in photovoltaic (PV) module manufacturing offers several significant benefits that enhance the overall performance, quality, and cost-effectiveness of solar panels. Here are the key advantages:
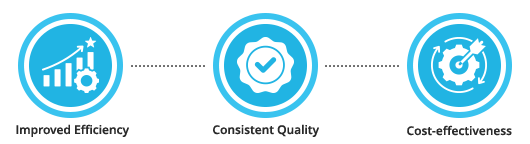
1. Improved Efficiency
Lamination machines ensure proper bonding of the layers within a solar panel, which is crucial for enhancing the panel's overall efficiency and performance. According to a study published by the National Renewable Energy Laboratory (NREL), high-quality lamination can result in efficiency improvements of up to 2-3% in solar panels . This enhanced efficiency is achieved through the protection of solar cells from environmental factors and mechanical stress, leading to improved energy conversion rates and longer-lasting panels. Consistent and uniform encapsulation minimizes the risk of air bubbles and impurities, which can otherwise reduce the panel's efficiency.
2. Consistent Quality
The lamination process is highly regulated and automated, aiming to maintain consistent quality levels in the manufactured solar panels. According to the International Energy Agency (IEA), advanced lamination techniques contribute to the production of defect-free panels, which is crucial for maintaining performance consistency over the panel's lifespan . This controlled environment ensures that each panel meets industry standards. For instance, the International Electrotechnical Commission (IEC) standards (such as IEC 61215 and IEC 61730) require rigorous testing for durability and performance, which high-quality lamination helps achieve.
3. Cost-effectiveness
While the initial investment in a lamination machine can be substantial, the long-term savings and reliability benefits often offset this cost. According to a report by the Solar Energy Industries Association (SEIA), the operational cost savings due to reduced maintenance and fewer replacements can lead to a significant return on investment over the lifetime of the solar panels . Additionally, the improved efficiency and consistent quality of the laminated panels contribute to higher energy yields, which translates to better financial returns. Over a typical 25-year lifespan, the enhanced durability and performance provided by lamination can save up to 10-15% in operational costs compared to non-laminated panels.
Why is Lamination Important?
Lamination serves several critical purposes in solar panel production:
1. Protection: The encapsulant layer safeguards the delicate solar cells from moisture, dust, and other environmental elements that could degrade their performance or cause failure.
2. Structural integrity: The lamination process creates a rigid and robust structure for the solar panel, ensuring it can withstand wind, hail, and other physical stresses.
3. Electrical insulation: The encapsulant acts as an electrical insulator, preventing short circuits and ensuring safe operation.
4. Improved performance: By eliminating air gaps between layers, lamination enhances light trapping within the solar cells, leading to better energy conversion efficiency.
Choosing the Right Laminator for Your Solar Manufacturing
Choosing the Best Laminator for Making Solar Panels Picking the right laminator for your solar panel production is really important for making sure everything runs smoothly and doesn't cost too much. Here are some things to think about when choosing a laminator, with lots of helpful information and advice:
1. Production Volume
High-volume manufacturers will likely favor fully automatic laminators for their superior efficiency and throughput. According to the International Energy Agency (IEA), fully automated systems can achieve production speeds of up to 600 modules per hour, significantly reducing the cost per unit. Semi-automatic laminators, on the other hand, are better suited for medium-sized production environments, with production capacities ranging from 100 to 300 modules per hour.
2. Encapsulant Material
The type of material used to encapsulate solar panels is very important because the laminator needs to work well with it. Some common materials used for encapsulation are Ethylene Vinyl Acetate (EVA), Polyvinyl Butyral (PVB), and Thermoplastic Polyolefin (TPO). EVA is the most commonly used because it sticks well and lasts a long time. However, newer materials like TPO are becoming more popular because they can resist UV rays better and require lower temperatures to process, which can help save energy.
3. Energy Efficiency
Energy usage is a big concern for many companies that produce goods. Fully automatic laminators, despite being able to produce a large quantity of items, can consume a significant amount of energy. According to a study by the National Renewable Energy Laboratory (NREL), fully automatic laminators use around 20-30% more energy than semi-automatic ones because they operate constantly and have advanced features.
4. Budget
The first thing to think about when buying a laminator is how much it costs. Fully automatic laminators are more expensive at the beginning because they have advanced technology and can laminate a lot of things quickly. Semi-automatic laminators are cheaper and are good for medium-sized businesses because they have a mix of automatic and manual features.
Additional Considerations for Solar Laminator Users
Beyond the basic types, several other aspects are crucial for solar laminator users:
1. Automation level: Laminators can range from manual to fully automated, with varying degrees of operator involvement.
2. Safety Features: Modern laminators have different safety features to keep people safe. These include emergency shut-off buttons, systems that check the temperature and pressure, and mechanisms to stop fires.
3. Maintenance: Regular maintenance of the laminator is very important to make sure it works well and lasts a long time. This means cleaning the heating parts, changing old seals, and adjusting the control systems.
Conclusion
Photovoltaic module laminators are really important for making sure that solar panels are good quality, last a long time, and work well. It's key for people in the solar energy business to know about how laminators work and why they're so important. If we keep coming up with new and better ways to laminate solar panels, we can make sure that they keep getting even better and last longer for future generations.